
Gas treating facilities, therefore, must be designed to convert a particular raw gas mixture into a sales gas that meets the sales-gas specifications, and such facilities must operate without interruption.
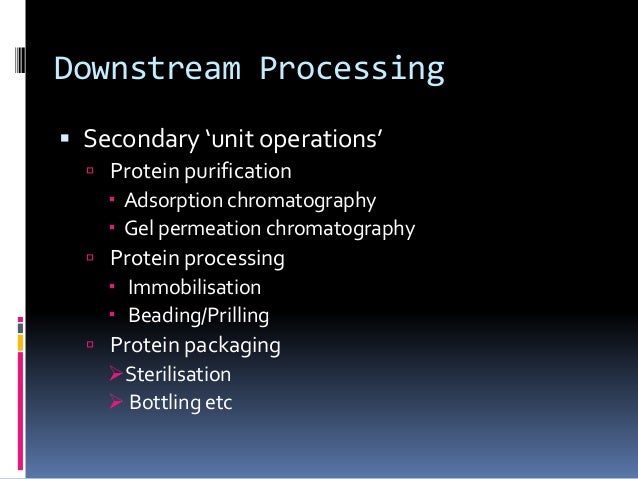
the supply of gas must be available at all times at the contracted rate.the gas must be of consistent quality, meeting sales gas specifications.The end user of natural gas needs to be assured of two conditions before committing to the use of gas in a home or factory: relative condensate/gas rates specifications for the residue gas and rate of gas sales.composition of separator inlet gas and condensate.the raw gas production capability to the plant.Objectives of Gas Treating and Processingīefore the optimum design of any gas treating plant can be decided, at minimum, one must know: 9.3 Nitrogen Recovery for Enhanced Oil Recovery.1 Objectives of Gas Treating and Processing.In addition to supplying the equilibrium data, these tests can reveal phase behavior near the liquid-liquid interface such as emulsification or entrainment that help guide extractor selection. When conducting an extraction pilot test, it is highly preferable to use actual plant feed and solvent materials.īefore pilot testing begins bench scale tests are performed to generate liquid-liquid equilibrium data. Dispersed phase entrainment, emulsification tendency and the impact of impurities at the liquid-liquid interface are some of the common phenomena that occur in an extraction column which makes pilot testing essential.
#Liquid liquid extraction in downstream processing software#
Unlike distillation processes, which can often be designed using process simulation and hydraulic rating software alone, extraction involves complex chemical phenomena at the liquid-liquid interface which is very difficult to model to allow for commercial scale process design. Nearly all extraction projects require pilot testing to provide the basis for commercial process design and a process performance guarantee. However, liquid-liquid extraction has become the standard for certain processes, such as the recovery of high boiling organics or non-volatile inorganics from dilute aqueous streams. Distillation is often considered first in the hierarchy of separations methods, and is taught extensively in chemical engineering curricula. Our liquid-liquid extraction / solvent extraction design expertise includes sieve tray columns, packed (SMVP) columns, pulsed columns, rotating disc contactor (RDC) columns, SCHEIBEL® columns, and KARR® columns.Īt Koch Modular, we do more than sell extraction equipment we supply solutions to difficult separation challenges.
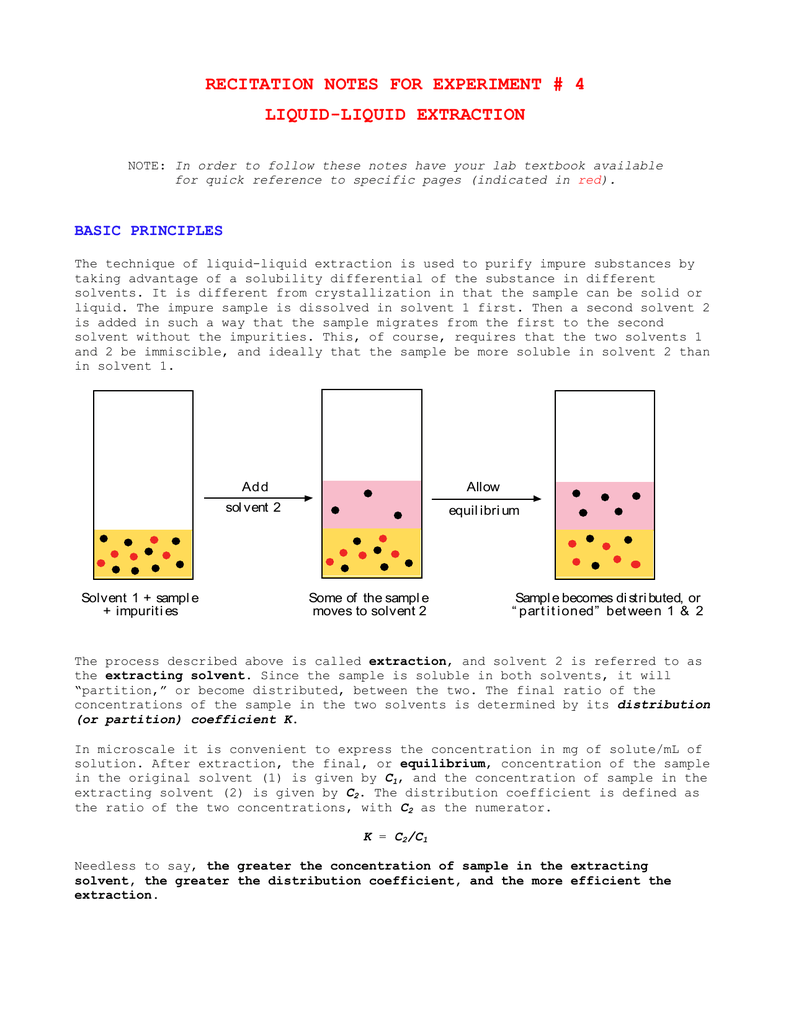
Our LLE / SX columns are engineered to fulfill the challenging purification requirements that exist in the alternative energy, biobased & renewable chemicals, flavor and fragrance, metals and mining, petrochemical and hydrocarbons, pharmaceuticals, polymers, and specialty chemicals industries. The Koch Modular Extraction Technology Group has decades of experience designing and supplying liquid-liquid extraction (LLE) / solvent extraction (SX) equipment.
